Epicor Advanced MES for Epicor ERP
- carolinechong7
- Aug 11, 2020
- 2 min read
Epicor Advanced MES for Epicor ERP
Manufacturing Execution System (MES)
Staying competitive isn’t easy in today’s evolving manufacturing space. How do you increase
efficiency and reduce costs while still complying with your customers’ requirements? That’s
where the Epicor® Advanced MES for Epicor® ERP comes in. Advanced MES utilizes Industry 4.0 technology on the shop floor — such as cyber-physical systems and Internet of Things (IoT) sensors - to help you gain the competitive advantage you need — both now and in the future.
Epicor ERP manufacturers use Advanced MES to improve quality, reduce scrap, help ensure
on-time delivery, and boost production throughput. It’s all about improving production
execution and performance efficiency to gain a competitive advantage. How do you make
more without more assets? Uncover and eliminate downtime to make more parts or cut costs.
Epicor Advanced MES can improve profitability by helping you find more capacity.
Epicor Advanced MES collects data directly from equipment and operators on the shop
floor in real-time, minimizing inaccurate and time-consuming manual data collection. With
information instantly in your hands, you can anticipate and solve production problems before they happen. Real-time insight helps you pinpoint critical issues, reduce waste, and improve quality and customer service. Everyone in the plant and throughout the business can take action to improve manufacturing performance.

📌 Production Monitoring
– Machine integration using OPC or IoT sensors
– Automatic data collection
– Monitor uptime/downtime
– Monitor actual cycle times and scrap

📌 Energy Monitoring
– Monitor and analyze energy
consumption by machine, job,
shift, or product
– Understand maintenance
and quality in the context of
energy consumption
– Analyze direct energy required
to produce any item.

📌 Planning and Scheduling
– Visual production scheduling and planning for machines and tools
– Automatic schedule adjustments
– Kanban scheduling.
– Labour and material requirements forecasting.
– Machine capacity planning.
– Tool conflicts.
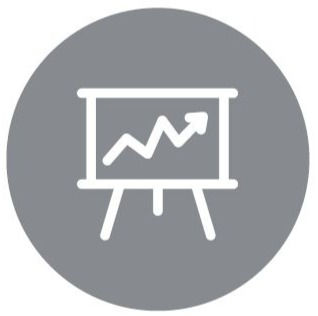
📌 Quality Management
– Automated process monitoring and parameter violation alarms
– Automatic part qualification/rejection
– Statistical process control (SPC)
– Statistical quality control (SQC)
– Monitor every cycle and every
machine 24/7
📌 Continuous Improvement (CI) Integration
– Lean
– Six Sigma®
– Theory of constraints (TOC)
– Total productive maintenance (TPM)
– Common and custom CI metrics
– OEE, asset utilization, and capacity utilization
– Meantime between failures (MBTF)
– Minor stops per runtime hour (MS/RH)
– Meantime to repair (MTTR)
– Root cause factors
Deployment Choice—On-Premises
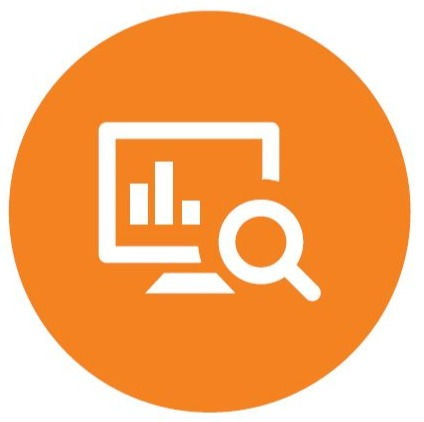
📌 Visibility, Reporting, and Analysis
– Automated overall equipment
effectiveness (OEE)
– Accurate, consistent
efficiency metrics
– Production metrics—from
machine to enterprise
– Downtime and scrap analysis
– Operator labour and productivity
visual root-cause indicators
– Real-time screens and views
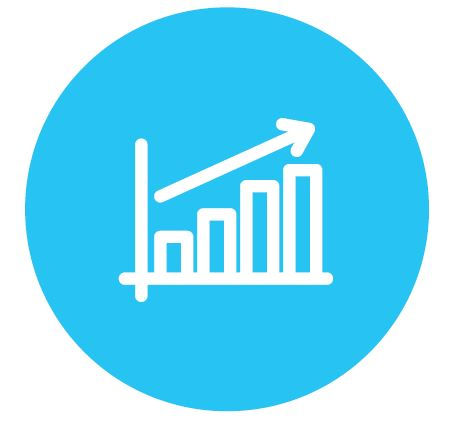
📌 Maintenance Management
– Preventative maintenance
for machines, tools, and
auxiliary assets
– Generate automatic
MRO tasks
– Schedules maintenance
around production
– Rules-based maintenance
based on runtime, cycles,
or time
– Real-time alerts and reports

Comments